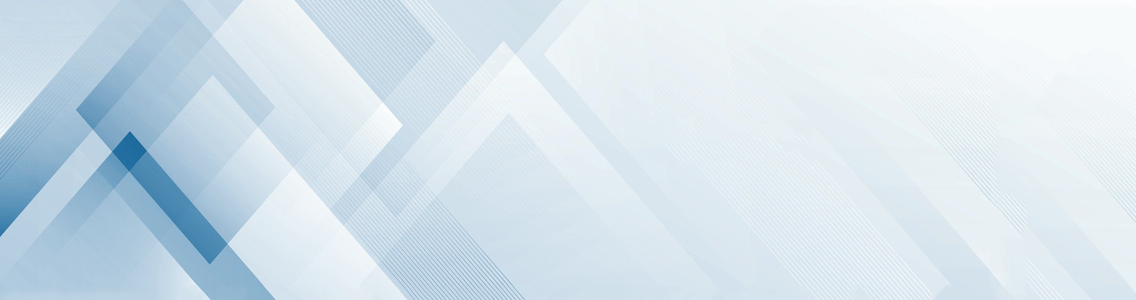
SERVICE
Steel Heat Treatment Experts | Vacuum Heat Treatment Factory
Vacuum heat treatment is a technology that involves processing objects at high temperatures in a vacuum environment. Its principles are based on thermodynamic concepts and mainly include the following aspects:
Steel is heated to around 1000 degrees Celsius and then rapidly cooled using nitrogen gas. This process enhances hardenability, adjusts hardness, and increases toughness. It involves cooling the steel after heating it to an appropriate temperature and is used to adjust the material properties of various steels, including tool steel, carbon steel, and alloy structural steel.
This process restores and improves ductility by eliminating work hardening, processing strains, and residual stresses in the material. Additionally, it can reduce hardness and improve machinability and plastic workability by removing strain, adjusting grain size and structure, and allowing for the diffusion and segregation of chemical components and impurity elements.
This process prevents the precipitation of carbides and intermetallic compounds at crystal and grain boundaries by rapidly cooling alloy components in a dissolved (solid solution) state. It enhances the corrosion resistance of austenitic stainless steels (such as SUS303, 304, etc.) by returning the deformation-induced martensitic structure to the gamma phase, thereby softening it.
This is a process that hardens the material either by disrupting the crystal structure in the solid solution state or by using newly precipitated elements and compounds from the supersaturated solid solution. This generally occurs after solution treatment and is used to strengthen high-strength copper alloys (such as beryllium copper alloys), heat-resistant alloys, and age-hardened stainless steels (such as SUS630, 631, 632).
Process |
Steel Types |
Quenching and Tempering |
Tool Steel (SKD), High-Speed Tool Steel (SKH), Alloy Tool Steel (SKS, SKT), Carbon Tool Steel (SK), High Carbon Chromium Bearing Steel (SUJ2), Martensitic Stainless Steel (410, 420) |
Age Hardening |
Beryllium Copper (Be-Cu) |
Solution Treatment |
Austenitic Stainless Steel (304, 316) |
Annealing |
High Carbon Chromium Bearing Steel (SUJ2) |
Precipitation Hardening |
Precipitation Hardening Stainless Steel (630) |